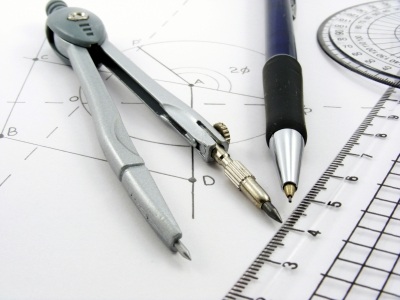
Make the right decision when you choose your moulded plastic parts and you set yourself up for a much easier time in the future. Make the wrong decision and it could end up costing you a lot in terms of money and time. When you want to use the injection moulding process to make plastic parts, follow this simple step-by-step guide to getting the right parts for your needs.
- Carry Out a Realistic Overview of Your Design
As far as you can, make sure that you understand how the part will work and how the design will allow it to function at its highest capacity. Take a look at the design to work out if there are any changes you need to make, any additions, or anything you need to take away in order to improve the design. Once you are convinced that it is fit for purpose, it helps to consult a professional in plastic injection moulding to make sure you are not overlooking anything.
- Choose a Suitable Moulding Company
Take some time researching different options in terms of companies to carry out the injection moulding process. The project will go more smoothly and you will be happier with the result when you trust the supplier, and can work well with them. Ask plenty of questions before you make a decision and if you are happy with the answers, meet in person to discuss your project in detail.
- Decide on the Right Plastic
Once you are working with an experienced company you can discuss crucial details like the correct plastic material for your needs. An experienced professional will ask questions to find out how the part will be used and where it will be used. Discussing all the possibilities for the item which will be produced helps to rule out any materials that are not suitable and to develop a list of materials that suit your purpose.
- Fine-Tune Your Design with a Professional
If you already have your design finalised, it helps to review it with the moulding company so that they can let you know if there are any alterations that could be made to create a smoother moulding process, or any additions that can be made at the beginning of the project that will save you money.
- Work Out Your Volumes
Understand the number of units you want to produce and communicate this to the supplier as getting your average order right helps to save you money.
- Look at a Prototype
Manufacturers like www.dataplastics.co.uk will produce a low-cost prototype that you can actually use in the application. By running a test with the prototype you can see if the part fits its purpose – and most times you can get a refund on the cost of the prototype if you go on to place an order.
- Check the Timing for the Order
Make sure you place your order in good time so that you ensure the manufacturer can meet your deadline. The deadline should be realistic so that you are not disappointed.