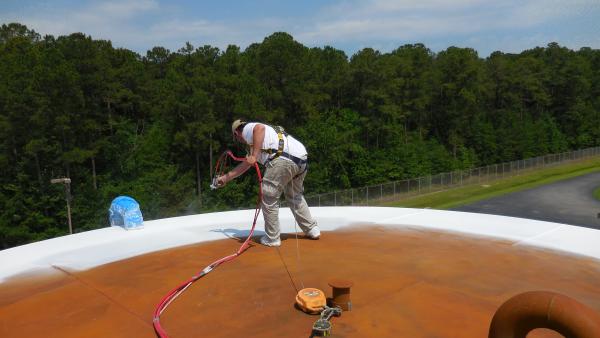
When applying coating on a metal surface, we could find a number of defects that happen when the coating has dried or cured.
- Incomplete or slow drying: It happens when the coating fails to harden or dried within a specified period of time. It could happen when a high performance coating isn’t properly mixed, causing insufficient chemical reactions. The drying additives may not be sufficiently added or mixed properly. When using a two-pack product, we should make sure that it has been mixed in a proper ratio. It is better to experiment and leave the coating on a small area of metal surface for about 24 hours. We should observe whether the coating has dried properly. If the coating is still tacky or soft, we would need to remove it using mechanical methods by scraping it. Use sandpaper to make sure that no coating is left on the surface. After we have discovered the proper mixture ratio and it has been stirred properly, we could reapply the coating.
- Discoloration: Surface discoloration could happen on surface that has been recently coated. This could happen when dirt settles on the coating surface. Resin could also break down due to chemical spillage or ultra violet exposure. Fading could happen when the coloring pigment breaks down. Rust staining happens when rust water runs down from nearby corroded areas. We should check whether discoloration can be removed by washing the metal surface with fresh water and mild detergent. If the discoloration and stains seem to be stubborn, we should abrade it lightly using find sandpaper.
- Corrosion: Even after if we have coated the metal surface, signs of corrosion may still emerge. This could happen when the coating somehow detaches from the metal surface. This could happen due to mechanical forces or other reasons. We may not adequately remove salt deposits before applying the coating or perhaps the coating is too thin. We could remedy this by localizing the affected area. Scrape the rusted deposits and remove the coating. Use needle gun or wire brush to remove any sign of corrosion. After the metal surface is clean of any deposit, we could reapply the coating. Try to give smooth overlap with the surrounding intact coating.
- Sagging: Sagging could happen when the coating is too thick, causing coating to slump on vertical surfaces. In this case, we should allow the coating to become completely dry. Use sandpaper to remove excess coating and produce smooth surface. Check the upper area for thin areas due to the sagging coating. Recoat when necessary.
November 9, 2016
797