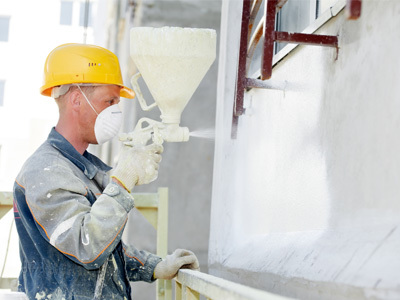
There are different types of anti corrosive coatings that we can use during a home improvement project. They are usually zinc dust, zinc phosphate, zinc chromate and red lead. By applying these coatings on the surface of metal, we should be able to minimize the overall spread of corrosion. Resins are among materials with the best electrical resistance, as well as chlorinated rubber, vinyl, phenol and catalyzed epoxy. In order to further increase the electrical resistance, the coating could be added with iron oxide, mica, china clay and talc. Before applying protective coating, we should remove any deposit on the metal surface, because it may short-circuit the resistance and rusting will still occur.
We should consider applying a thicker coating to further increase the electrical resistance. Coating prevents salt, water and oxygen from contacting the metal surface. It means that the protective coating works as a barrier. Materials that have the lowest permeability to oxygen and water are chlorinated rubber, vinyl, polyurethane, coal tar epoxies and catalyzed epoxies. So, if we are living in a relatively wet climate, we should consider using these materials to prevent rust on metal surface. These coatings should also provide additional protection against chemical fumes, skid, abrasion, high temperature and fire. Again, budget has a major factor in determining what kind of coating we should choose.
Conventional coating is often available as a single pack product, while high performance coating comes in two packs. Single pack products can work with only air drying, while two-pack products require chemical reactions to be fully cured and hardened. For better results, we should contact manufacturers that provide specialized coatings for certain purposes. As an example, a coating could work well for decorative purposes on metal surfaces, while others purely intended for heavy-duty industrial usages. Coating can be applied using airless spray, conventional spray, roller or brush. The last two are used when airless or air sprays are not suitable to our conditions.
Rollers and brush are suitable when we want to apply thicker coating on metal surface. However, using both can be quite slow and we may only be able to cover limited surface of metal. Air spray is suitable when a thin application is sufficient and we want a quick result. When applying anti-corrosive coating, we should avoid doing it during an adverse condition. The temperature should be no higher than 35 degrees C or lower than 5 degrees C. The surface shouldn’t be wet due to condensation, fog, ice, snow or rain. Read the instruction on how to handle anti-corrosive coating. As an example, the coating may need to be stirred first to disperse solids.