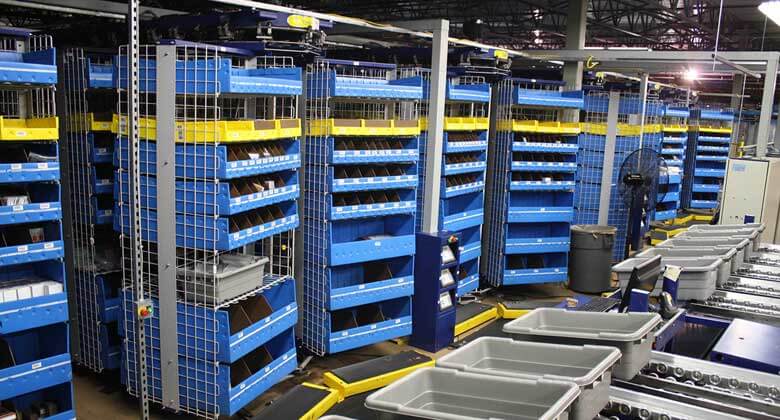
Just in time manufacturing is a method that is used to reduce a company’s inventory and streamline their production processes. In a traditional business model, items are manufactured and then sent to storage to wait for a customer order to fill. Some of the downsides of this more traditional model include that companies will need more space for inventory and that they may have a surplus of items, which tends to lead to increases in rent and carryover expenses for products that have not yet sold. Just in time manufacturing is a cutting-edge solution to this problem that came well ahead of its time.
Just What is Just in Time Manufacturing?
Just in time manufacturing is designed to follow an on-demand model, meaning that products are not created before they are needed. This was first discussed by Henry Ford in his book My Life and Work, published in 1923. He noted how the Ford Company purchased only what the company needed for current items to reduce excess inventory and cut out the waste of materials and labor that is associated with overproduction. While computerized sales and asset tracking were still some decades away from truly realizing the potential in this simple but nonetheless revolutionary idea in Ford’s time, the realities of the manufacturing and fulfillment industries as they exist in today’s world not only make this a possibility, they make it a necessity.
How Does This Save Time & Money?
As orders come in, you have the items necessary to manufacture them shipped to the factory. As the product moves through the stages of production, those parts are efficiently moved directly to the workstation that needs them, at the exact moment they are needed in the process. The drawback of this method is that companies may be ill-prepared if bulk orders or a sudden surge in orders happens, so a small supply of carried over materials is still recommended. But this is also where modern information technology sweeps in — we live in an age where we can plan for demand better than ever before, and better understand our business needs at every step in the process before we even reach it. This allows automated storage and retrieval systems to use their optimized storage capabilities to the best advantage of the production, storage, and fulfillment processes of your business.
Are You Ready for ASRS?
An automated storage and retrieval system (AS/RS) like the vertical lift module is designed for a number of reasons. First, it allows you to easily access inventory, even those stacked on the highest shelves on your system. This safely optimizes the retrieval process. Second, it reduces the amount of space needed for inventory because the items can be stacked so high. Finally, the system improves safety in storage areas, because there is no manual labor needed to retrieve an item — the item is delivered right to the hands of the worker who needs it by the storage system, itself. Likewise, asset-tracking reduces waste, losses, and other errors and inefficiencies by streamlining the role of the human operator.
These automated storage and retrieval systems can also be customized to suit the needs of your business and the places they will occupy in your production and fulfillment process. Everything from layouts and bay sizes to temperature and climate control can be designed to specification. If you’re looking for ways to save on your storage or production costs, or simply wish to streamline your fulfillment process, automated storage and retrieval systems like the lift and carousel systems offered by Vertical Storage USA are ideal. Talk to their service specialists about how your business can benefit from modern ASRS technologies.